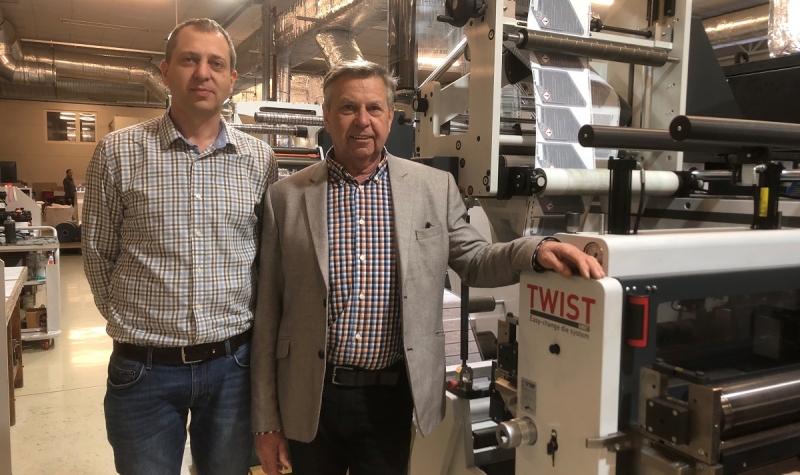
Druk-ker, Hungary: “Our vision is the added value of partnerships: we found it with OMET”
Druk-ker Nyomdaipari Kft is a Hungarian company founded in 1992 as a family business. Specialized in offset, digital and flexo technologies, it’s the shrink sleeve leader in Hungary. They have built their success on reliability and quality of its products, following each customer in his specific needs with great competence. In 2019 they installed an OMET X6.0 for the production of shrink sleeves, IML, self-adhesive labels. In this interview, Péter Markó, the current managing director and son of one of the founders, tell us about their growth path.
Mr. Markò, when did your company start its business?
During the period of state socialism there were no private printing companies in Hungary, therefore my father Mr. János Markó was a self-employed entrepreneur doing only embellishment. After the change of regime, my father together with his friends started the company: Mr. Tibor Horváth, as investor, Mr. János Markó and Mr. Sándor Péntek as printers and Mr. János Dorogi who did the sales.
Mr. Dorogi left the company and I took his place before becoming the production manager in 2010 when my sister Mrs. Annamária Markó took over the management of the office. Currently Mr. Péntek is the head of Technical Department, Mr. Horváth is still a co-owner, my father and me are the managing directors.
Druk-ker has now over 70 employees, over 3000 square metres headquarters in Kiskőrös and a sales office in Budapest.
Could you describe the stages of your company development to the present day?
The company started with embellishing and letterpress printing, then we invested in small sheet-fed offset machines to print documents and envelopes with 1 colour, relatively quick. We had our first 4 colour offset press in 1996 to produce marketing materials and labels: this was the way for a continuous growth. Geographically we are located in the middle of the biggest wine region of Hungary, so the label business developed nicely. In 2004 we purchased a UV offset press in order to improve our print quality and to increase the production volume of our marketing products. This turned out to be a good decision, because fortunately the market of premium marketing products did not collapse during the world economy crisis of 2008. The demand for rolled self adhesive labels and also for labels printed on foils never slowed down, so we followed this direction during the crisis. We started roll-to-roll UV flexo printing in 2010 with a 410 mm web-width press. Together with the printing machine we purchased machines for converting and embellishment, beginning a smooth moving from sheet-fed to roll-to-roll labels. In 2011, we also started to print shrink sleeve products.
Was it a fast growing market?
Rolled label and shrink sleeve markets was rapidly growing: we outgrew our site, which we have been constantly expanding before, but we reached the limit.
We purchased an existing production hall, we fully modernized it and we moved our flexo production there. In 2014, we had 2 production sites, one for roll-to-roll UV flexo and the other for sheet-fed offset printing. At the beginning, it was OK, but after one year, we already needed to change. We had to face too many logistic issues, so we started developing and expanding a new site. Luckily, we could manage to increase the size of our land, having enough space to build new offices and a warehouse. Moving the production is always difficult, because you have 2-3 weeks of downtime. The solution for us was 2 new installations: we could stop and move the existing machines after the new machines were arrived. Year 2019 was a big milestone, we installed a Heidelberg XL 75-5L UV sheet-fed offset machine and an OMET XFlex X6.0 530 press. Our increase in printing capacity brought the need of a converting section as well, so we installed new shrink sleeve seaming, inspection, cutting machines and an IML die-cutting machine.
Our aim was to build a stable production site, with at least 2 machines for each production process. Nowadays we can proudly say that we are the leading shrink sleeve producer in Hungary, but the most important thing is that we can serve our valued customers for any kind of labelling technologies.
How and when did you meet OMET equipment?
We have been always attending the most important fairs and exhibitions of the label industry, so we could see the amazing evolution of OMET, who became one of the biggest and most advanced press manufacturers. XFlex platform attracted us immediately when presented to the market.
When did you decide to invest in OMET technology?
We had to wait for the right moment with the right circumstances. As you can see from our brief history, our last 10 years were very busy, full with different type of investments. In 2015 we had the chance to buy a used XFlex X6 430 press. We were very satisfied with the performances, so in 2018 we decided to invest in a new X6.0 530 machine.
Which was the reasons why you choose another OMET machine?
We were very satisfied with the performance of our X6 430, especially in terms of tension control and register stability. We appreciated the possibility to have customized solutions: it was very convincing to see the wide range of different special options offered by OMET. Also the provided support was very quick and flexible. Last, but not the least, we have always had a very good relationship with Printline, who is the local representative of OMET.
How is your investment in the OMET X6.0 helping you to develop your business?
Investing into OMET brought more efficiency to our production. Thanks to the sleeve technology and the Twist die system, we can do very quick job changes, so we have less downtimes. With the automatic register control system we have less setup waste and better register stability. The automatic pressure adjustment system makes it easier to recall repeating jobs.
What type of substrates are you using?
We use self-adhesive paper and clear on clear materials, BOPP unsupported film, PVC and PET shrink films. The perfect tension control and automatic register control system help us to precisely handle very thin (12-15 micron) unsupported filmic materials.
How much work do you produce each year (volume or value)?
Our total turnover is about 3,8 MEUR (50% roll-to-roll, 45% sheet-fed, 5% digital). Material consumption: 150t shrink film and IML, 800.000m2 self adhesive.
What are your future plans?
Our dream would be to have a hybrid rotary offset and flexo press on the X-Flex platform, but first we should see our financial possibilities and the upcoming market demands.