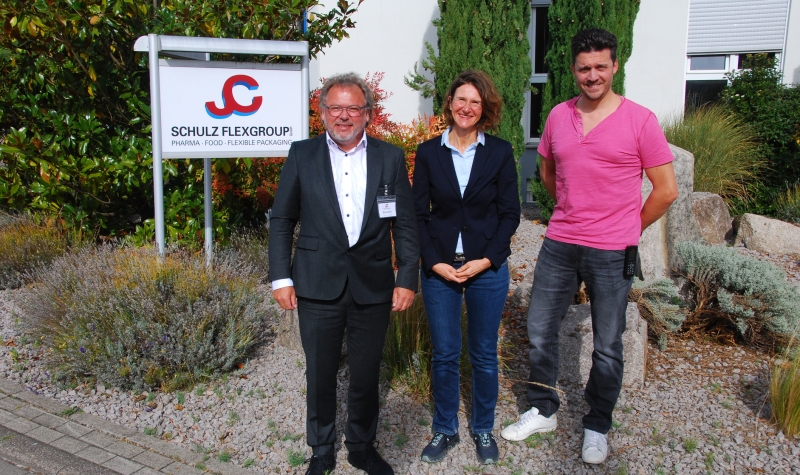
Bravely take new paths
Schulz Flexgroup GmbH is breaking new ground with the installation of three OMET XFlex X6 for printing blister packs.
If you want to be successful in competition, you have to leave the beaten path. Although it seems to offer security, it is also the place where the most traffic occurs. Schulz Flexgroup GmbH took an unusual path with the investment decision for UV flexographic printing machines from OMET – and with success. In this article, the company owner and managing director Cordula Schulz and Vincent Lavorato, Technical Managing Director, explain why the company, specialized in flexible packaging, has installed a total of three XFlex models designed for label printing at its two locations in Baden-Baden and Roth in recent years.
A contact with a colleague in a label printing company brought Vincent Lavorato closer to the type of machine common to the narrow web industry for the first time. In the basic concept of the OMET printing line used there, he recognized a suitable solution for his own task in the blister packaging industry. Current customer demands and the trend towards smaller runs were becoming increasingly difficult to meet with the existing machine technology – aging flexographic printing machines in a row design.
When the customer convinces the supplier
Before Vincent Lavorato could put the first OMET machine into operation in July 2021, he had to overcome a few obstacles. Schulz Flexgroup is a packaging printing company with a fleet of mainly central cylinder flexo printing machines in web widths of up to 1400 mm – and not a label printing company. That is why company owner Cordula Schulz was initially skeptical about the project. However, she was convinced by the various advantages. In addition to shorter set-up times, the OMET technology also promised less physical strain on the operating personnel. Vincent Lavorato knew from his own experience the effort involved in changing complete cylinders, including gears, as he himself used to work on the machine as a printer. In addition, other features such as the short web guidance through the OMET machines open up opportunities to reduce waste and material consumption. “The concept of the in-line machine and the web width of 530 mm are very well suited for our orders from the pharmaceutical industry. Processing aluminum foil with larger widths increases the risk of wrinkling.”
Vincent Lavorato was aware that various technical adjustments would be necessary due to special requirements when printing pharmaceutical packaging. But they seemed entirely feasible. That is why he and Cordula Schulz were surprised when their inquiries about supplying a three-color UV flexo printing machine caused a lack of interest from potential machine suppliers. The manufacturers blocked the idea by pointing out that corresponding machine models could only be produced economically if they had a larger number of inking units.
Third machine in three years
One company that took on the task, although it had initially hesitated given the special requirements, was the machine manufacturer OMET from Lecco, Italy. As Cordula Schulz remembers, the persuasive work that Klaus Sedlmayr, managing director of Chromos Deutschland GmbH, did in this project also contributed to this. The trading company from Augsburg supports OMET in terms of sales and service on the German market.
In the meantime, the situation has changed significantly. The Schulz Flexgroup group has now installed a total of three OMET XFlex X6. The first two were set up at the Baden-Baden location in July 2021 and May 2022. Each of them is equipped with three printing units with a web width of 530 mm. With these two machines, the print shop now achieves a higher production output than with three previous systems that they replaced.
Save expensive energy and resources with a new machine
The purchase of the third OMET was a very short-term decision. When the costs for energy and nitrogen rose to unimaginable heights at the end of 2022, the idea arose to also install an OMET machine at the Roth location. After all, the first two plants in Baden-Baden had proven their advantages in terms of efficient use of energy and materials. UV lamps and inert gas technology from PrintConcept enabled noticeable savings, especially when it came to nitrogen consumption. After nitrogen, which is used as an inert gas to operate UV curing, had become more expensive by over 200 percent at this point and a calculation showed a return on investment (ROI) in a period of just over two years, the decision was made by Cordula Schulz quickly for the installation of the third OMET XFlex. “However, the decision is only partly based on economic reasons,” explains Cordula Schulz. “In the medium term, it is also an important step on the way to CO2-neutral production.”
Thanks to increased energy efficiency and reduced emissions, the company has made great progress on the path to carbon neutrality. “We accept the challenges surrounding sustainability and are always proactively looking for solutions,” says Cordula Schulz. This ranges from recyclable film and paper packaging to self-supply of energy, for which Schulz Flexgroup invested almost one million euros in photovoltaic systems at both locations two years ago. This means that more than a third of the electricity consumed is currently generated internally. Since 2022, 480,000 kg of CO2 emissions have been saved. All measures are embedded in the company’s ERP system, which is currently being completely restructured. “The digitalization of all processes establishes a strong foundation for the future. We see ourselves as a model medium-sized company. We will keep the workforce of around 110 employees stable and at the same time generate sustainable growth through further digitalized processes.”
Solution-oriented for mutual success
To ensure that the installation of an OMET XFlex in the Schulz Flexgroup environment would ultimately be mutually beneficial, Klaus Sedlmayr believed that a solution-oriented approach was essential from both parties. Since neither OMET nor Chromos had any experience of how a machine designed for label printing behaves in this new field of activity, the supplier side was dependent on constructive cooperation and non-judgmental feedback when implementing the first installation. “We received a lot of positive input from Schulz Flexgroup with numerous ideas for practical optimizations, so that in the end we were able to fully meet our expectations,” says Klaus Sedlmayr, looking back. As an example, he cites the special requirement to integrate existing UV inert gas curing into the machine. Vincent Lavorato in particular suggested solutions where the necessary space for installation should be structurally provided. In the end, all sides benefited from this professional dialogue.
For Cordula Schulz, this type of solution-oriented collaboration is self-evident: “Treating customers, employees and suppliers as equal partners has been the DNA of our company for decades. Living this consistently also requires mutual trust because the partnership is equally demanded by the other side.”
The partnership-based collaboration with customers manifests itself in daily practice through intensive application-related advice. The order is preceded by a detailed analysis of the requirements profile. The suitability of film materials, inks, varnishes and sealing processes for the respective filling goods is checked, as is their ability to be processed on the packaging machines. The color management system is also individualized and can be based on a sample, Pantone fan or reference card.
Trust in the technology
The company’s trust in its delivery partner is evidenced by the order for the third machine, which was recently installed in Roth. While various improvement requests had to be implemented with the first, for the third machine was not even needed the acceptance testing in Italy. After the Chromos Germany team had completed the assembly in Roth and the printing staff had been prepared for the new machine with a four-day training course, production began immediately. “Since then,” says Vincent Lavorato, “the machine has produced flawlessly.”
The fact that OMET machines have a high level of printing stability is a particularly important criterion for Vincent Lavorato. Corrective action rarely needs to be taken in production, which allows staff to work stress-free. In addition, the printers in all OMET installations responded very positively to the change from the previous machines to the new ones, as they offer noticeably improved ergonomic conditions. For example, the fact that there are no heavy parts to lift and the machines run more quietly is something that even the company doctors at Schulz Flexgroup expressly praise.
A further improvement comes from the type of ink supply, which in the OMET machines takes place without ink pumps. This enables significant savings compared to previous machines because previously a minimum amount of ink had to be mixed to create a proof. With small runs, larger amounts of ink residue always arose.
Machine concept enables conditions similar to digital printing
When Schulz Flexgroup started looking for a suitable machine system for printing blister packs, the focus was on a high level of flexibility to be able to guarantee short delivery times for small and medium runs. This requirement is becoming increasingly important because print runs have been falling for years and, above all, product cycles are continually becoming shorter. With the Omet XFlex, the company has found a machine system that can compete with digital printing, as Cordula Schulz shows: “The break-even point, including clichés, is in the range of 1,500 linear meters. The setup and operation, as well as the feasible delivery times, make it almost comparable to digital printing for our special applications. That is why we can accept print jobs that customers previously preferred to print digitally. The only exception are jobs with personalization, which hardly play a role in our market segment.”
Exemplary entrepreneurship
The investment in three printing lines from OMET gives an impression of Cordula Schulz’s understanding of leadership. She is very aware of the tricky challenges that companies in Germany are currently facing. Personally, however, she prefers the focus on the diversity and development potential of medium-sized companies. Since there is no way around change anyway, she calls on entrepreneurs to be more courageous. German medium-sized businesses in particular offer the best opportunities to continue to be successful in the future. It is particularly important to her that she sees a company as an ideal platform for being able to be successful together with people. The economic medal for outstanding services to the Baden-Württemberg economy, with which the state of Baden-Württemberg awarded Cordula Schulz in 2022, shows that this type of entrepreneurship also develops external appeal.
Successful family business in the second generation
Schulz Flexgroup GmbH is owner-managed and a specialist in the printing and finishing of primary packaging for the pharmaceutical and cosmetics industries and for technical and non-food applications. At the two locations in Baden-Baden and Roth near Nuremberg, the company achieved sales of 32 million euros in 2022 with a total of 117 employees in two-shift operation. In 2013, the current owner and managing director Cordula Schulz took over the company from her father Jürgen Schulz, who founded the company in 1977.
In 2003, Cordula Schulz joined the medium-sized family business. From 2011, she ran the plant in Baden-Baden and finally took over complete management in 2013. In 2020, she appointed Vincent Lavorato, the long-time Production and Operations Manager, as Technical Managing Director. Together they renewed the entire machine park at both locations within a decade. In the last five years, investments in new machines and operating equipment amounting to around 10 million euros were made. During this time, specialization in the pharmaceutical industry was also promoted, so that the bottom line was that growth increased by 66 percent. Orders from the pharmaceutical industry currently represent the largest customer segment at 85 percent. The rest is shared by the cosmetics sector with 10 percent as well as technical and other applications.
Schulz Flexgroup’s technical equipment includes ten printing machines with a total of 43 inking units. The range extends from single-color to eight-color machines in web widths from 200 mm to 1400 mm. Twelve rotary cutters are used in the cutting operation for widths of up to 600 mm.
by Klemens Ehrlitzer