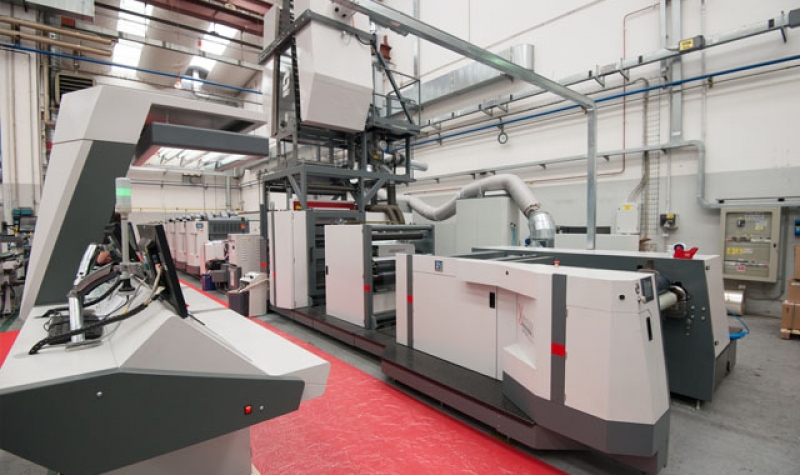
Varyflex V4 Offset: OMET to introduce the future of flexible packaging
Flexible packaging owns the future. Adaptable packages fitting the products. Colorful space-saving cases, resealable and safe, spreading on the shelves and becoming more and more appreciated by the producers and the consumers thanks to user-friendly logistics, use and recycling.
Moving with the future means to invest in technology development and OMET has never given up on it: this is part of its DNA since 1963. This is the message behind the Open House “Your Passport to Packaging” organized by OMET on the 20th and 21st March, which gathered some of the most important players of the sector as well as the major specialized newspapers. The event was the occasion to launch the new Varyflex V4 Offset: a mid-web machine featuring OMET patented offset technology combined with in-line flexo units, the first of its kind to lead the way towards a premium quality, flexibility and a consistent cost reduction.
Numbers do not lie. Packaging is the leading sector of the entire global printing industry, overcoming commercial and editorial products. Moreover, flexible packaging is destined to become the main segment of the packaging market: with a 25% share and a CAGR (compound annual growth rate) forecast of 5.1%, it is about to pass the board segment, reaching a turnover of $ 126 Billion[1]. This potential growth is led by the “Food & beverage” sector. In Europe, almost 90%[2] of food packaging on the market is flexible: sachets, stand-up pouches, squeezable and resealable cases and so on. Asia-Pacific and Latin America represent a great market potential offering big margins of penetration due to the lack of modern packaging systems.
In this context, the key words to success are flexibility, quality and safety. Flexibility is a major trend due to the increasing request of packaging versioning to satisfy targeted marketing initiatives and demand a premium price. In fact, flexible packaging offers higher printability and extended personalization capability, with the possibility to produce value-adding packages with different shapes and sizes to reach the target with higher precision.
As a consequence of the increasing product customization, print runs and time-to-market tend to shorten: production lead-time and costs have become two crucial factor to be competitive on the market. Yet, the quality of packaging cannot be scarified, since it is essential when it comes to maximize the appeal on the shelf and drive the choice of the final consumer. Last but not least, safety it is one of the focal points for the success of flexible packaging, as it provides high barrier properties and improves products preservation.
According to Flexible Packaging Association, flexible packaging allows for the reduction of 91% of raw material and could save 96% of space when empty: it is estimated that almost 3 times more units fit on a standard pallet. This means an easier logistic management and a drastic reduction of waste: this aspect has been drawing the attention of the global industry for the last years, both in terms of efficiency and eco-friendly approach.
“Offset technology is the best solution to ride these market trends – explained Marco Calcagni, OMET commercial director -. The low cost as well as the short lead-time preparation of the plates allow for quicker and more frequent job changeovers, crucial advantage to be responsive to market necessities without profit reduction. It provides more flexibility compared to rotogravure or flexo printing, whose printing tools could take days or even weeks to be available and ready to print. For short and medium runs, offset technology is absolutely the most cost-effective solution, combining low production costs to high quality results, especially with CMYK printing, vignette printing, light/dark areas and fine lines”.
Varyflex V4 Offset features 33”1/2-wide offset groups with OMET patented sleeve technology, combined with new fully automatic flexo units able to reach a maximum mechanical speed of 400 m/min.
Thanks to the integration of the Electron Beam curing system and to low-migration inks, Varyflex V4 Offset is the perfect solution for food packaging printing, with no risk for ink and solvent residuals on the packs.
Every offset unit features the “Easy Sleeve Format Change” system, with independent pressure adjustment and automatic register control, which allow quick and easy job changeovers in few minutes. This press is designed to work in different configurations: Wet-On-Dry with interdeck UV curing or Wet-On-Wet with UV or EB curing at the end of the line. The configuration showed in the Open House was composed by 7 offset groups plus one flexo Wet-On-Wet with EB curing, with the addition of another Wet-On-Dry flexo unit with hot air drying system.
“We chose to implement the Electron Beam system because of its high-curing properties especially on complex job with full-color printing – explained Mr. Calcagni-. It was a choice driven by the increasing requirement of packaging safety especially in the food and cosmetic sectors, where strict rules discipline the utilization of specific materials and inks that could come in contact with alimentary or dermatological products. Generally speaking, Varyflex V4 Offset is a high-competitive machine in a market where runs are getting shorter and shorter and the alternative technologies, like rotogravure and CI flexo, has higher production costs and are not flexible in terms of process and configuration”.
In other words, Varyflex V4 Offset was designed to anticipate the necessities of the market and lead the companies towards the future. With this line, OMET widens its products range and consolidates its leading position in the flexible packaging market, providing an answer to the widespread need for added value and customization. The main features of the machine obtained sincere appreciation during the Open House, showing once again the reasons why OMET is one of the leading companies of the packaging printing market.
[1] Research and markets, “Flexible packaging market – global forecast to 2021”
[2] http://www.macchinealimentari.it/2015/08/31/flexible-packaging-mercato-vivo-e-novita-interessanti/