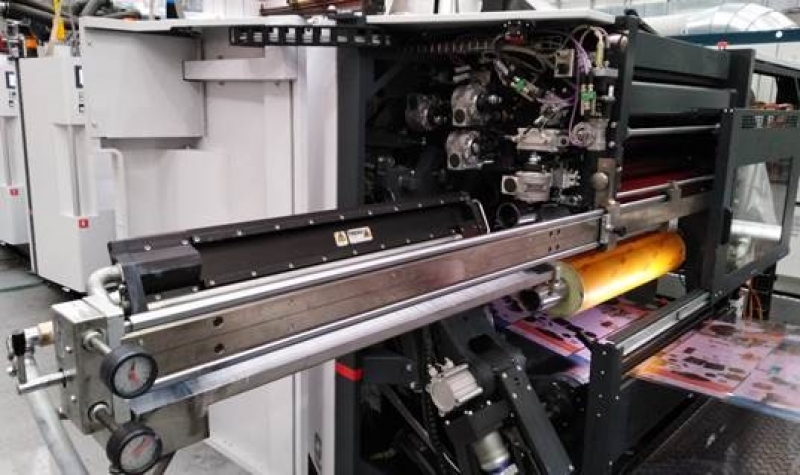
UV web offset printing is one of the current trends in packaging printing
The interest in this technology is caused by its technological features, by development of UV technologies, combination of various types of printing and converting inline for production of labels and packaging , requirements of the quick set up and change over processes.
Advantages of offset
The main advantage of offset is the highest print quality. Offset offers the highest screen lines and lowest dot gain of any printing process available. High-quality printing of halftones, images with high contrast, thin lines and texts using only four printing units determine the high position of offset in the field of printing technologies. Offset printing is well studied, mass-produced and standardized. This ensures high repeatability of results and an incomparably easier way to produce first-class raster images.
There is also a big difference in the cost of offset plates compared to flexographic photopolymer plates. The approximate ratio is 1 to 7. There is no need for expensive double-sided adhesive tape used for mounting photopolymers on the plate cylinders. It is also important that the speed of production of metal offset plates (15-20 min) is superior to common methods of production of photopolymer plates. Due to the absence of direct contact between the printing plate and the material, offset printing allows working on some materials with rough surface (e.g wine paper material). The ink is transferred to the material from the blanket and there is less risk of clogging the plate. Offset printing is characterized by a wide variety of consumables from different manufacturers.
Offset with dampening
When we talk about offset printing with UV inks in OMET machines, we use wet offset printing. This printing principle is based on maintaining a balance between ink and water (dampening solution) on the aluminum plate. The printing elements are wetted by the ink and repel water, while the blank elements, on the contrary, are damped by water and repel ink.
Rotary or semi rotary
For OMET rotary machines, format change is achieved through the rapid replacement of plate and offset sleeves. The machines use servo-drive technology, which eliminates the dependence of printing formats on the pitch value of the gears.
The advantage of fully rotary machines over semi-rotary machines is higher productivity. The speed differs greatly. To give an example of the maximum speed of the OMET machine when working in rotation mode with interchangeable sleeves reaches 300 m/min, when working in semi-rotation mode the speed will be about 50 m/min. The second advantage of rotary machines is a wide range of choice of printed materials, from films to cardboard, so in rotary machines there is a wider range of tension settings and less strain on the tension in the machine.
It is possible to print monofilms for flexible packaging, such as PP, shrink materials, Inmold and others. By offering sleeve technology, OMET offers a more cost-effective solution than interchangeable format cassettes, which is important to consider when calculating the investment in the machine.
Offset, flexo, rotogravure? OMET combines different types of printing inline
Each printing method has its advantages and disadvantages. In order to obtain the highest quality of printing and reduce the cost of production, OMET offers combined machines integrating different printing units, including offset, flexo, rotogravure. This solution of printing and finishing lines allows to take only the best of each type of printing!
For comparative analysis, let’s take a combined OMET machine and a typical sheetfed press with a UV coating section.
The sheetfed offset machine itself is cheaper than the web press, but if we also take into account the sheetfed finishing equipment that is necessary to produce the final product, the situation changes to a more economically attractive one for the rotary printing and finishing line.
Undoubtedly, the main advantage of a rotary press will be the possibility to make various finishing operations on the printing press itself. In one working cycle we can get products with die-cutting and foil stamping, with varnishing or lamination, screen printing, perforation, creasing, embossing , longitudinal slitting and lateral sheeting, etc.
Minimum operators !
Minimum set-up waste!
Minimum production area !
Highest flexibility!
Convenient logistics without the need for an intermediate warehouse !
The next major advantage of rotary presses is their versatility in the choice of the material to be printed. We mean the possibility of printing on flexible packaging materials that are completely inaccessible for sheet offset printing, such as polymer films, foils, laminates. The use of roll materials reduces the cost of production.
Such equipment will allow a sheetfed printing house together with its customer to switch, for example, from production of paper labels to production of PS labels and filmic stock without learning a new printing technology.
Quick change of order, small runs, less time for production and assembly of plates
Offset plates today are produced immediately . The cost of an offset plate is less than 20% of the cost of a flexo plate and even less of the cost of a laser-engraved gravure cylinder. Offset has no limitations in screen and minimum dot size, which means much higher and more consistent quality.
The offset order changeover is carried out in less than 1 minute per unit, so that a complete machine set-up can be carried out by one person in a few minutes. The pneumatics open the clamps on the offset sleeves and they can be easily removed with the Revolver cart. New RFID plate and offset sleeves are clamped by vacuum and servo drives place them precisely in the register position. The print mechanical speed of 400 m/min is significantly higher than on narrow web flexo presses.
Examples of configurations for printing packaging and labels
Can be different configurations on the base of the modular machines of OMET . For instance , infeed module is followed by a flexo unit used for primer and applying special coatings. This is followed by 4-5-6-7-8 offset units, which are dedicated for raster printing. The offset units are followed by a desired number of flexo units for varnishing or printing with special, e.g. high pigmented, metallized inks. Cold foil , UV lamination units can be in any flexo position. The hot foil stamping and screen printing units are independently motorized and can be moved along the machine on the rails. Machine can be equipped even with solvent laminating unit and gravure in explosion proof performance and can run with digital modules.
It is important to mention that the OMET Varyflex offset model has the option of replacing the offset printing unit with flexo printing which gives full flexibility .
As the final processes can be used converting, finishing units, rotary die cutting or even cutting into sheets with further stacker or shingling device.
Machine has an advanced Vision automatic register control system, remote control of ink zones, automatic tension control system, automatic washing system , 100% inspection control system etc.
Offset printing on films
The main advantage is standardized offset quality. The use of sleeves is a common technology in flexography. It is now also used in OMET offset machines . The change of sleeves is also very fast. Thus, machine can print packaging with offset quality with infinitely variable printing lengths. Printing widths of Varyflex are 430, 530, 670, 850 mm.
Traditionally packaging has been printed by gravure or flexo printing, but nowadays it is printed also by offset. When choosing one or another printing technology it is necessary to evaluate not only the initial investment, but much more importantly, how much money can be earned. For example, for a print run of 10 thousand m2 offset can be 40% cheaper than printing on CI flexographic and gravure printing machines.
Why to use Ebeam curing ? This technology has 4 fundemental advantages:
Varyflex Offset unit is characterized by ground-breaking features making it the most revolutionary offset unit on the market today, including different types of curing: UV wet/wet, UV interdeck, EB wet/wet.
UNIQUE OFFSET GROUP DESIGN
• Axis of the plate mandrel with fixed center to improve printing precision through the increase of the group rigidity
• Wide range of printable materials from 12 micron film to cardboard.
• Offset plate sleeves with skewing adjustment to correct the small misalignments of the plates directly on the press
• Pneumo-locking light sleeves made of plastics, aluminum or carbon fiber
• Revolver cart for sleeves facilitating quick format changeovers; the sleeves are aligned with the group mandrels ready for format change and slide into position. No need for the operator to lift heavy weights!
• Due to the high automation and design of the printing press, quick set-up for print runs and fast changeover.
• Direct-drive, water-cooled, ‘torque’ type sleeve shaft and counter cylinder motors
• 10 different motors on each printing unit
• Inking train with 20 rollers plus extra roller that maintains wetting separated from inking
• Vision-2 register control system, both machine and cross side
• Extra unit stiffness for no vibrations transmitted onto the Offset plates
• LED-Illuminated unit chassis
• Automatic on-board plate washing
• Available web paths, drying and curing systems: UV wet/wet, UV interdeck, EB wet/wet
Author of the article
Tatyana Gaponova / Export area manager of OMET srl.