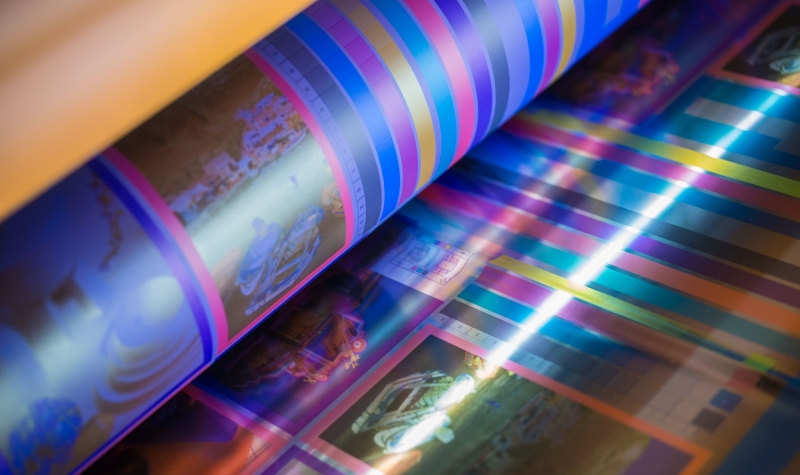
The importance of automatic register adjustment
The most important step to achieve an efficient job set-up is the REGISTER ADJUSTMENT operation, which must be fast, precise and reliable.
At every job changeover, after having placed and pre-registered the printing equipment, the operator must adjust the register mark of every color, one by one, until he they reach the perfect registration.
This operation can be done either manually or through semi-automatic electronic controls. However, the operator can only focus on one color at the time, causing consistent unproductive time and set-up waste, which lead to costs.
To reduce this inefficiency all OMET servo presses are equipped with a unique patented system able to replace eyes and hands of the operator by performing a perfect automatic register adjustment in the shortest time possible: The Vision system.
The OMET Vision system is a fully automatic and operator-independent register adjustment control based on a multi-scanning camera placed at the end of the line which reads specific circular marks printed by each color and tells the system their position compared to the center of the master color. When the operator pushes the button, the Vision system automatically corrects the position of the circles and obtains the perfect register in few seconds.
Thanks to OMET Vision system, the register adjustment operation does not depend anymore on the skills of the operator and becomes a fully automatic process which excludes any possible human mistake and delay. The machine is no more an operator-based solution, but turns into a system-based solution.
Register control and gate function
We often hear about “gate function” but sometimes there is not much clarity regarding this topic.
During the printing process, there are always direct or indirect factors that may affect the register stability. The machine could warm up because of the speed, the UV or other external factors such as humidity and temperature. Thus, the material, especially filmic substrates, may stretch and change the initial condition, affecting the print result.
To keep the register stable for the whole run without the intervention of the operator, most servo presses feature Mark-to-Cylinder Register Control and only few Mark to Mark Register Control.
In Automatic Mark-to-Cylinder systems, the register control monitors the stability of the printing position according to the initial setting, by checking through high-precision photocells an eye-mark applied on the printed image. If the position changes, the register control communicates to the motors to move accordingly.
Since the mark printed on the side of the web may take some printable space up, in a few particular cases like yogurt lids application, when the pattern requires wider space or the substrate is expensive, it is possible to position the eye-mark inside the printing pattern in the matrix area, thus saving space on the edges of the web. This specific function is called GATE and it is available on all OMET servo presses. It works with both register control’s eye-mark and Vision’s register marks, allowing the maximum flexibility.